Precision-Crafted Foam Interiors
Expertly designed to cradle your equipment, each foam insert offers a snug fit, ensuring maximum security for your valuable gear.
NANUK Custom Foams
Tailored to Fit Your Every Need
NANUK custom case solutions further expand your horizons. Foam interiors, printing, paneling, and custom coloring all contribute to a case fully equipped for the job.
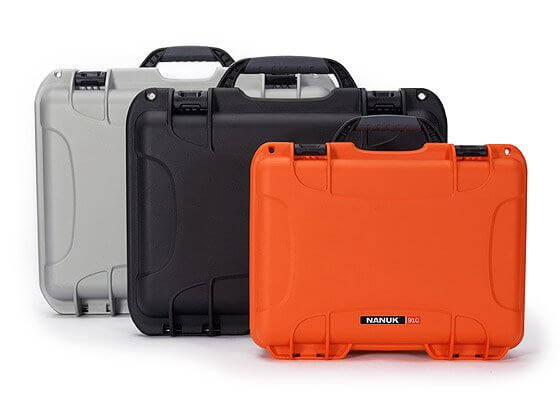
Select Your Case
Case selection is the first step in the custom foam design process. Depending on your project requirements, you may need a case that’s tough and waterproof with a lifetime warranty—NANUK is the case you need. Looking for something stylish and affordable? Our Designer series may be the way to go. Once the case is chosen, the final step in the selection process is to decide on a color.
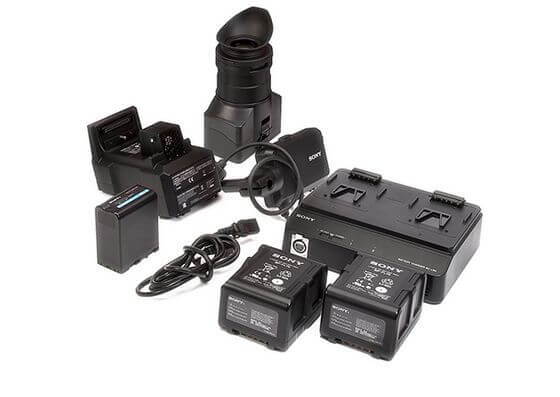
Send your drawings and components
To begin the design process we require drawings, in either 2D or 3D format, that accurately represent the shape and size of the items that will be placed inside the case. When possible, we prefer to have the components shipped to us prior to starting the design process. This allows us to physically test the fit of the components in the case and it reduces the time required to finalize the design.
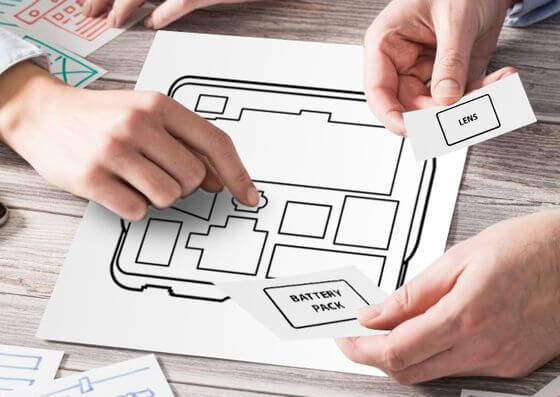
Tell us about your preferred layout
If you have a specific layout in mind, you can let us know with a drawing or an email description, but we can also suggest the most effective layout based on your requirements. Occasionally during this process, we will need to move to another case size in order to allow for enough foam to protect your equipment.

Foam Selection
NANUK offers a variety of different types of foam for your project. Foam selection is usually dictated by three factors: the level of protection required, aesthetic appeal, and price. The foams that we typically use fall under three material families: polyurethane (PUF), polyethylene (PEF), and Ethylene-Vinyl Acetate (EVA).
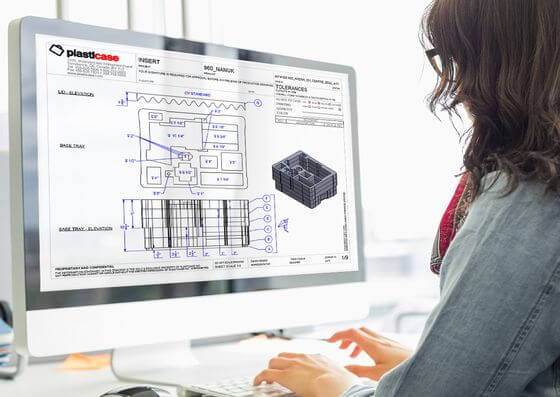
Develop drawings for customer review
Once we have all the technical information required to proceed with the design process, our team of designers will prepare a set of drawings to clearly illustrate the layout of your equipment inside the case. These drawings will also indicate all engineering details required to manufacture the foam. Your representative will send you the drawings for preliminary approval to proceed to the prototype phase.
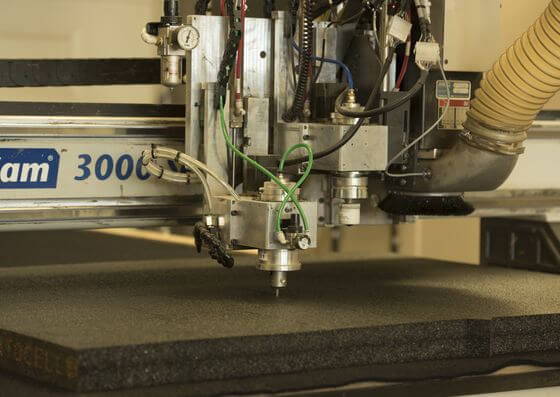
Prototype production
Once the drawings have been reviewed and accepted by the customer, we will produce a prototype to confirm fit and function of the design. Our engineering department will review the prototype to confirm that the foam meets the initial requirements. Once the prototype has passed our internal QC inspection, we will ship the foam to you inside the case for review.
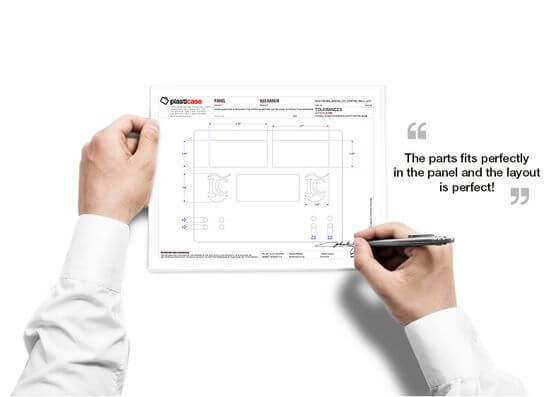
Customer Approval
Your Sales Representative will arrange to have the prototype shipped to you for review and approval. If the prototype is to your satisfaction, simply sign the provided production approval drawings in order to proceed to the start of production. Occasionally, it may take several revisions and/or prototypes to get the proper fit.
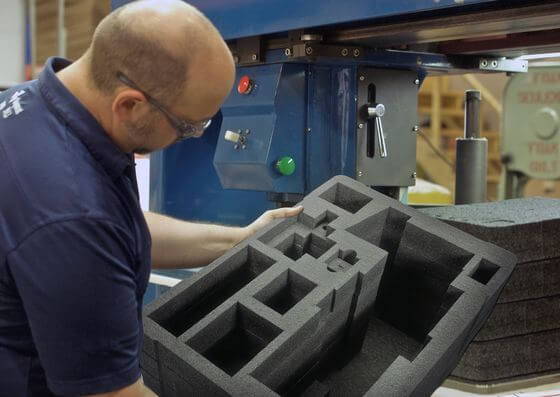
Production
Once the foam design is approved we can move towards production. We employ two different methods of foam manufacturing either CNC Router for Low-volume runs or Die Cut for higher volume runs.
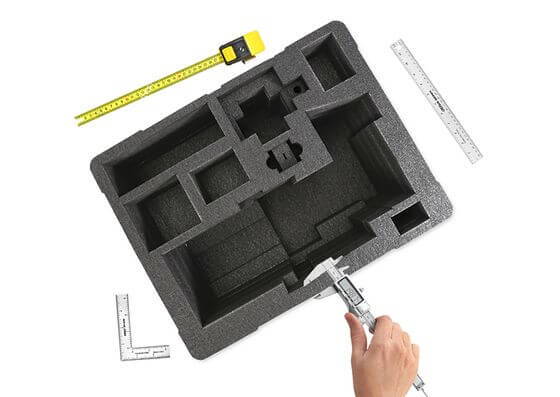
Quality Control
The foam production process is constantly monitored to ensure a consistent quality throughout the production cycle. Important elements that are verified during the QC process include: material integrity, cavity profiles, and depths,along with fit within the case. Our strict document control process ensures that all unique specifications to your project are clearly indicated to ensure that each production meets your expectations.
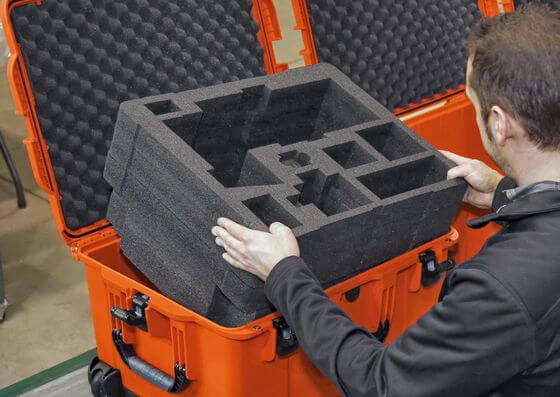
Final Case Assembly
After the foam has received its final QC approval, it can proceed to the final assembly stage. Depending on your requirements, the foam can either be glued inside the case or left loose. A final QC check is performed to make surethat the case meets your requirements and is then ready to be shipped to your door.
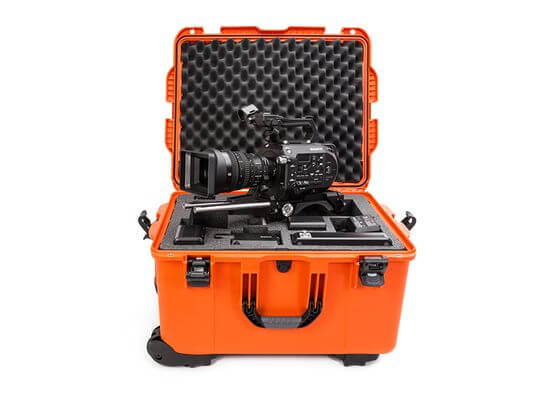
Finished Product
Whether you need 10 or 10,000 cases, NANUK has the expertise to deliver a complete case solution on time and on budget.
Select Your Case
Case selection is the first step in the custom foam design process. Depending on your project requirements, you may need a case that’s tough and waterproof with a lifetime warranty—NANUK is the case you need. Looking for something stylish and affordable? Our Designer series may be the way to go. Once the case is chosen, the final step in the selection process is to decide on a color.
Send your drawings and components
To begin the design process we require drawings, in either 2D or 3D format, that accurately represent the shape and size of the items that will be placed inside the case. When possible, we prefer to have the components shipped to us prior to starting the design process. This allows us to physically test the fit of the components in the case and it reduces the time required to finalize the design.
Tell us about your preferred layout
If you have a specific layout in mind, you can let us know with a drawing or an email description, but we can also suggest the most effective layout based on your requirements. Occasionally during this process, we will need to move to another case size in order to allow for enough foam to protect your equipment.
Foam Selection
NANUK offers a variety of different types of foam for your project. Foam selection is usually dictated by three factors: the level of protection required, aesthetic appeal, and price. The foams that we typically use fall under three material families: polyurethane (PUF), polyethylene (PEF), and Ethylene-Vinyl Acetate (EVA).
Develop drawings for customer review
Once we have all the technical information required to proceed with the design process, our team of designers will prepare a set of drawings to clearly illustrate the layout of your equipment inside the case. These drawings will also indicate all engineering details required to manufacture the foam. Your representative will send you the drawings for preliminary approval to proceed to the prototype phase.
Prototype production
Once the drawings have been reviewed and accepted by the customer, we will produce a prototype to confirm fit and function of the design. Our engineering department will review the prototype to confirm that the foam meets the initial requirements. Once the prototype has passed our internal QC inspection, we will ship the foam to you inside the case for review.
Customer Approval
Your Sales Representative will arrange to have the prototype shipped to you for review and approval. If the prototype is to your satisfaction, simply sign the provided production approval drawings in order to proceed to the start of production. Occasionally, it may take several revisions and/or prototypes to get the proper fit.
Production
Once the foam design is approved we can move towards production. We employ two different methods of foam manufacturing either CNC Router for Low-volume runs or Die Cut for higher volume runs.
Quality Control
The foam production process is constantly monitored to ensure a consistent quality throughout the production cycle. Important elements that are verified during the QC process include: material integrity, cavity profiles, and depths,along with fit within the case. Our strict document control process ensures that all unique specifications to your project are clearly indicated to ensure that each production meets your expectations.
Final Case Assembly
After the foam has received its final QC approval, it can proceed to the final assembly stage. Depending on your requirements, the foam can either be glued inside the case or left loose. A final QC check is performed to make surethat the case meets your requirements and is then ready to be shipped to your door.
Finished Product
Whether you need 10 or 10,000 cases, NANUK has the expertise to deliver a complete case solution on time and on budget.
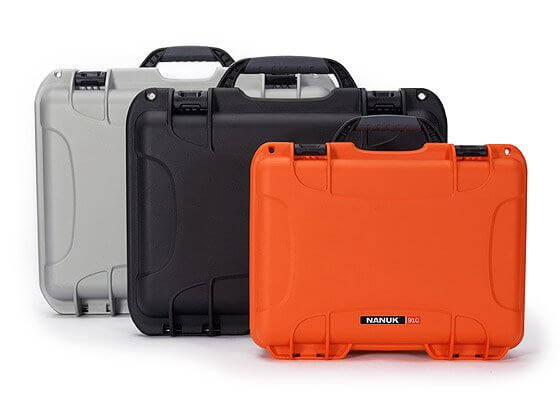
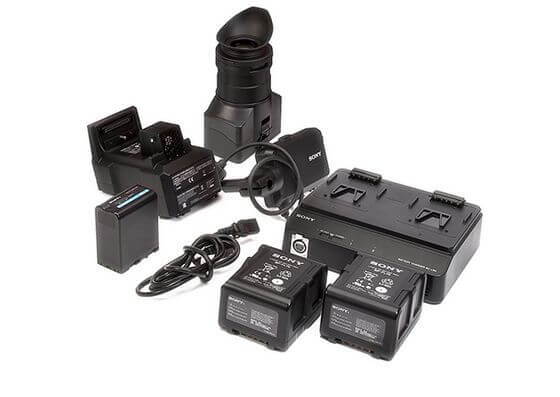
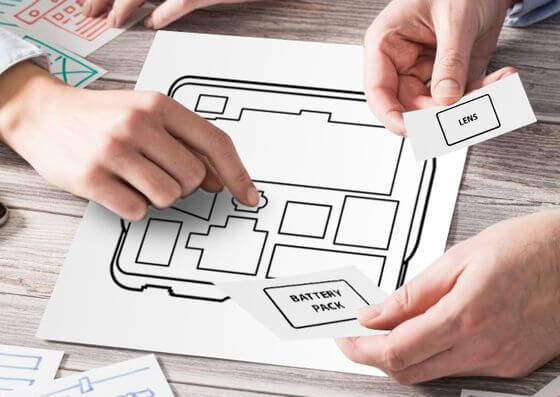

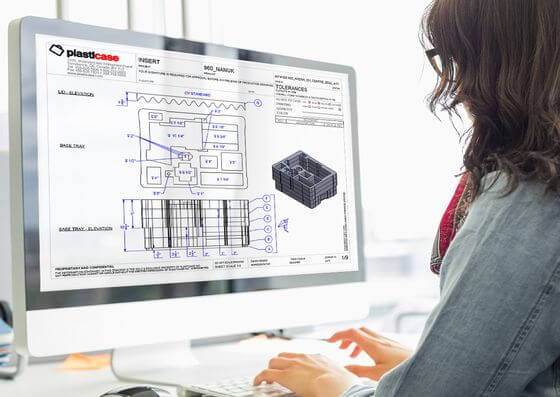
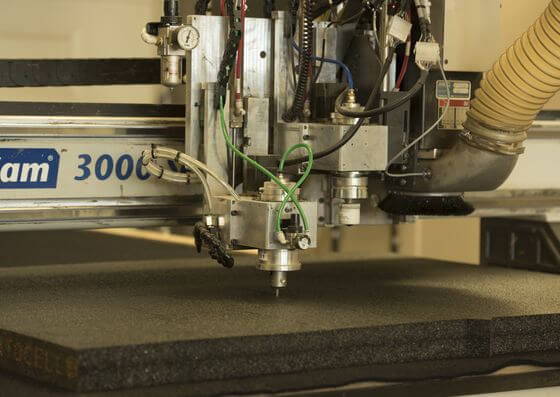
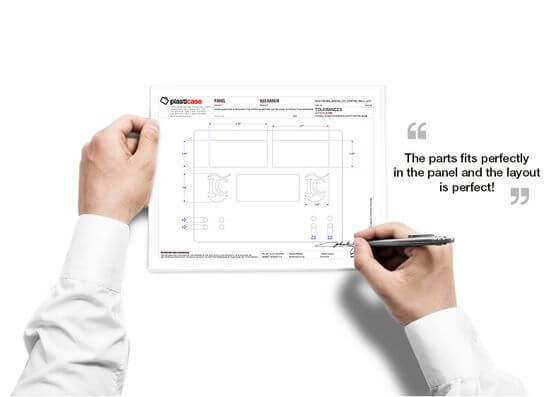
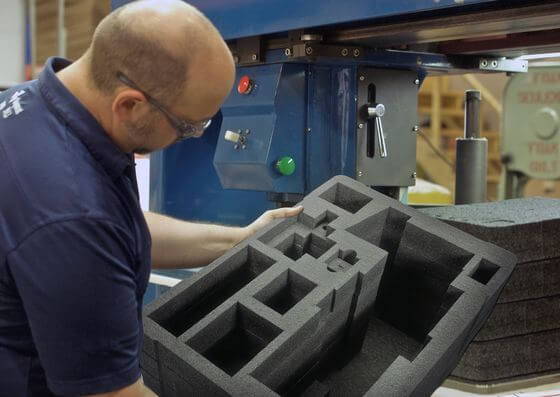
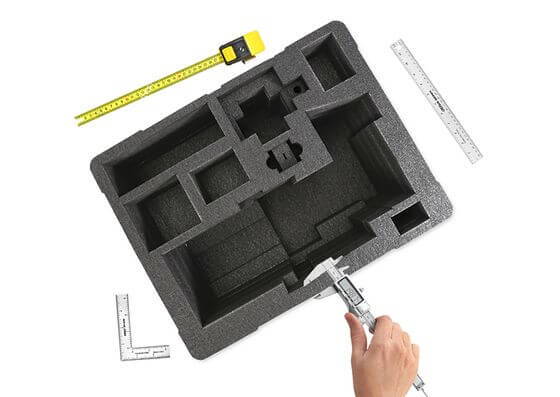
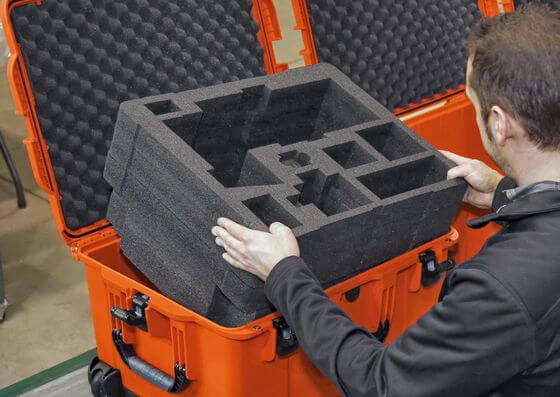
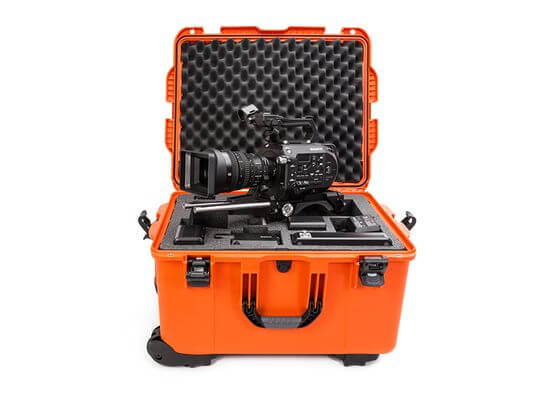
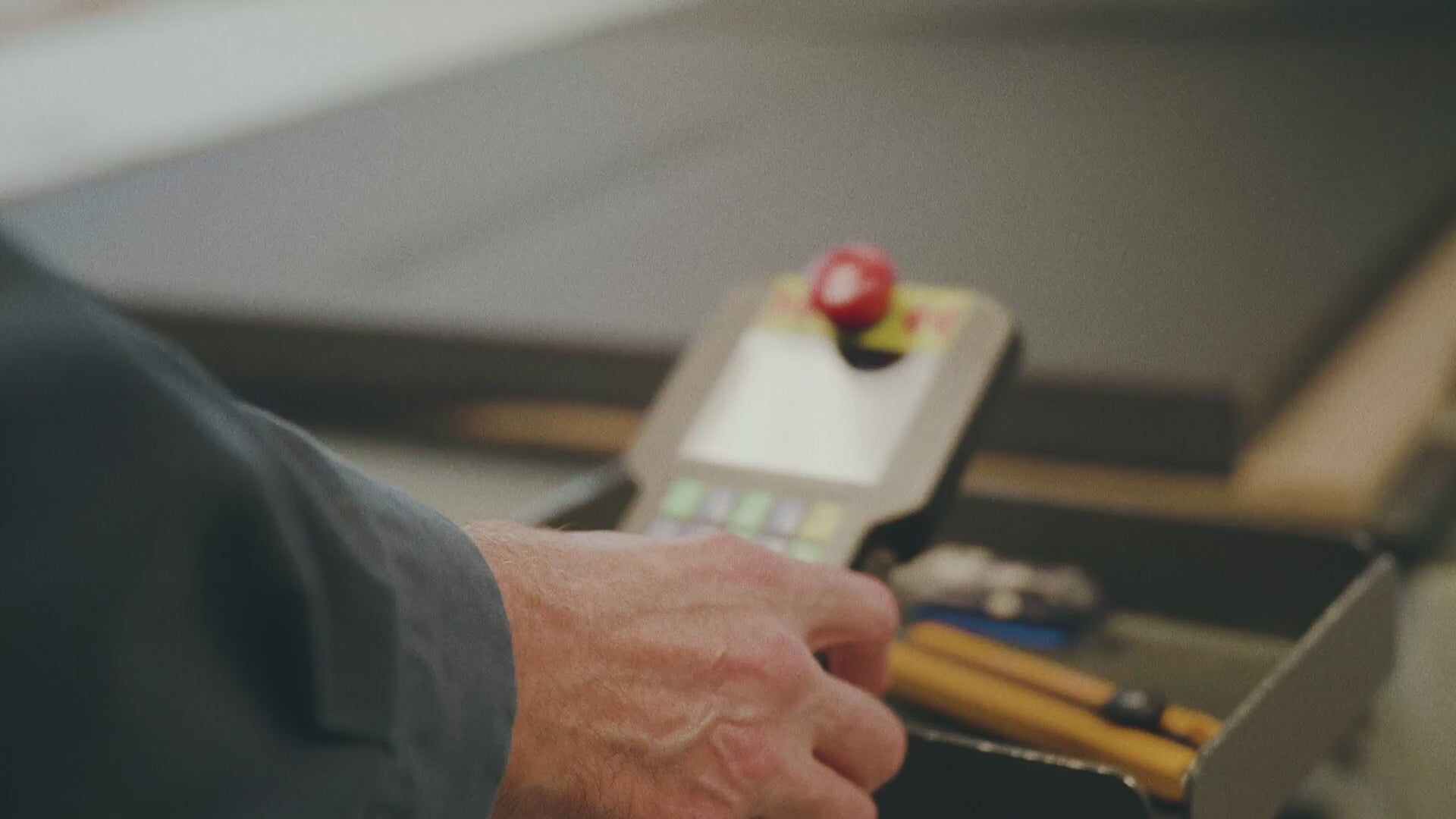
Start the Process
Customize Your Foam Interior Now
Don't settle for generic. Craft an interior that’s as unique as your gear. Tailor-made precision is just a few clicks away. Step into the world of bespoke safety today.